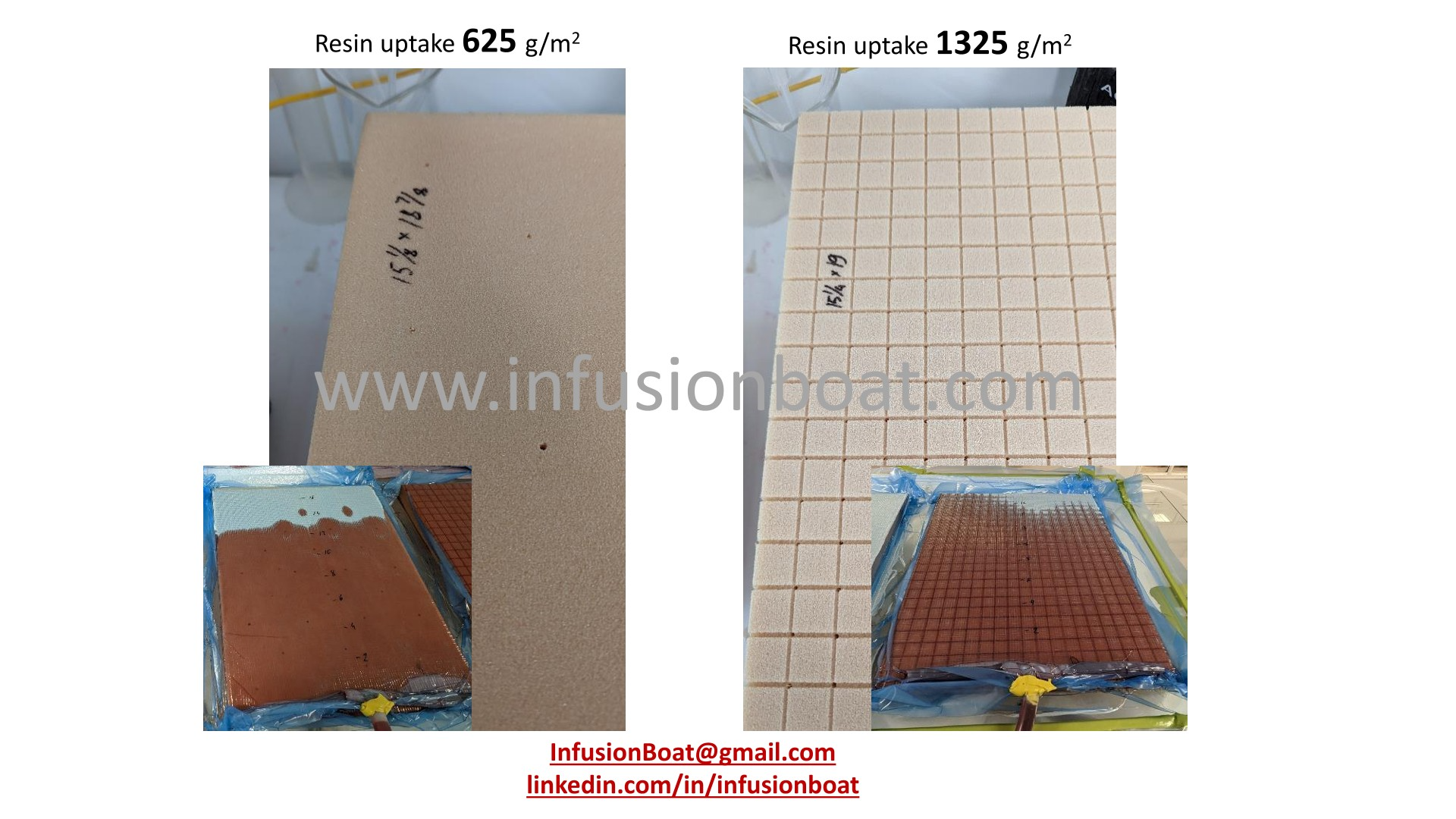
This example demonstrates the resin uptake capacity of foam. Resin uptake by foam is influenced not only by the foam's finish but also by its porous structure.
Foam with holes and grooves exhibits twice the resin uptake compared to foam with just holes. However, it's important to note that the presence of resin in these grooves and holes does not improve the mechanical performance of the sandwich structure. In some cases, it can even worsen it, such as in high-energy impacts.
It is believed that the grooves in the foam expedite resin vacuum infusion. This holds true when the right technology is employed. However, in reality, almost all foam manufacturers can supply foam with holes that do not align with the grooves, rendering the use of grooved foam with holes pointless. Some boatbuilders address this issue by adding mesh to the process. Consequently, during the initial stage of part infusion when the resin flow rate is very high, additional resin lines need to be added, resulting in extra costs. As a result, the amount of resin used unnecessarily may exceed the required amount for impregnating the reinforcement.
The best approach is to take this parameter into account during part design and the development of the manufacturing process. Incorrect infusion can result in a part with the same weight, and the overall part cost can exceed that of using the hand ply method. Therefore, when designing a part, it is crucial to choose the right foam, fabrics, and process. Only then can you fully enjoy the benefits of infusion.